Best-in-class industrial robot
Konstanz, October 8, 2024 – After the successful market entry of the HORST1500, the first industrial robot of the new generation of digital robots, Fruitcore Robotics is presenting the HORST1000 G2 for the first time at Motek in Stuttgart. The second robot of this new generation combines innovative drive technology with intuitive operation and AI Copilot. The HORST1000 G2 is quick to install and program, requires no expertise and offers the best lifetime cost on the market.
Technology leadership through innovative drive technology
With a load capacity of up to 16 kg, the HORST1000 G2 is the most powerful robot of its size on the market. Like the HORST1500, this robot features a unique patented drive technology that is maintenance-free and particularly cost-effective, significantly reducing service life costs. A six-year warranty on the drivetrain highlights the reliability and cost-effectiveness of the system.
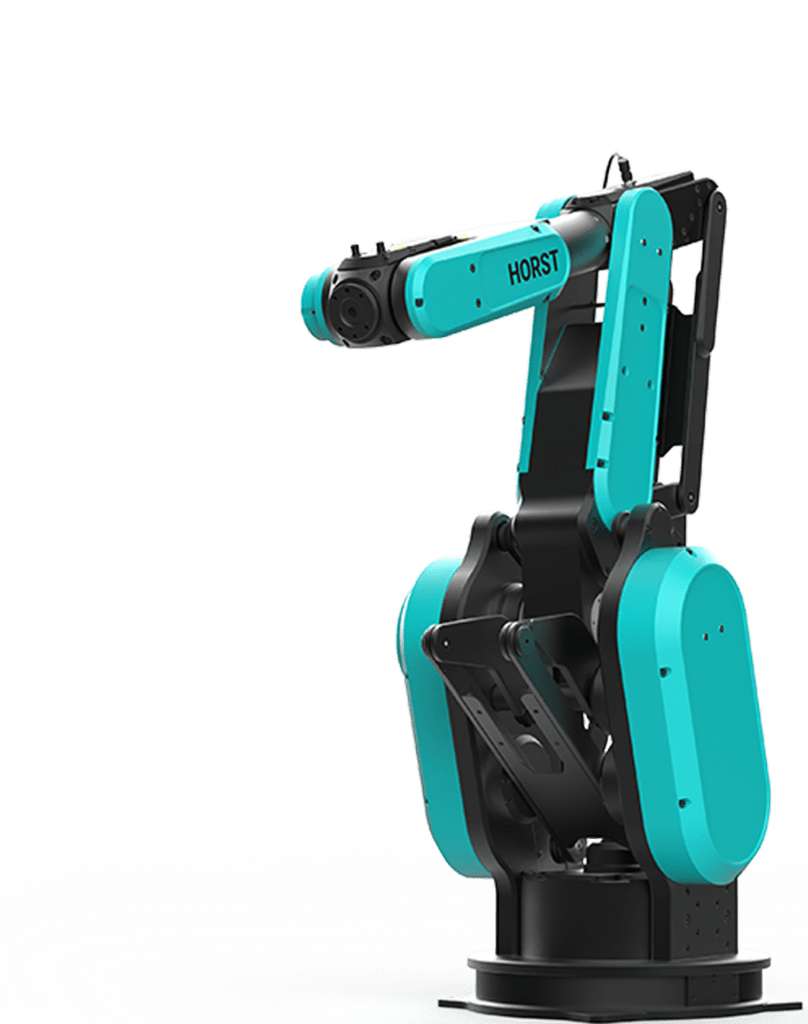
“Our technology combines innovation and economic added value, making automation accessible to a broad user base,” says Jens Riegger, CEO of Fruitcore Robotics. “Companies that use our robots achieve impressive ROI in just a few months and gain a clear competitive advantage.”
Intelligent control and safe human-machine interaction
The highlight of the new generation of digital robots is AI Copilot, integrated into the control software that gives the robots cognitive abilities. This technology allows users to communicate with robots in real time and solve complex tasks quickly and accurately with AI support. AI Copilot not only simplifies support, but also helps with specific programming tasks. This provides greater flexibility and significantly reduces reliance on experts.
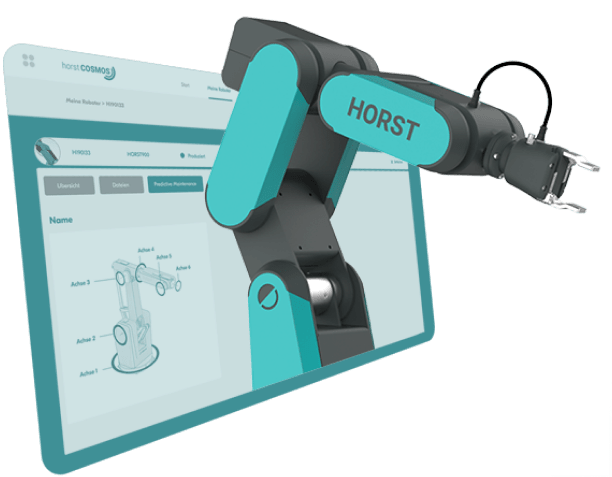
Additionally, HORST1000 G2 is equipped with advanced safety solutions designed to ensure safe use by humans. Like all robots from Fruitcore Robotics, this robot can operate safely at reduced speeds and with safety sensors, without the need for a protective fence. They are also available as ready-to-use solution kits that meet all safety requirements and save valuable time on CE compliance.
Optimized for machine tending and harsh environments
With a reach of 1141 mm and a payload capacity of up to 16 kg, the HORST1000 G2 is optimized for machine loading and parts handling tasks. Easily move heavy tools and components across your entire work area. The robot is equipped with protection class IP54. It is ideal for harsh production environments.
Thanks to its compact design, the HORST1000 G2 can move close to the machine and reach deep into it, significantly increasing flexibility in constrained production environments. The robot handles work surfaces up to 450 x 900 mm or square-shaped trays up to 520 x 520 mm.
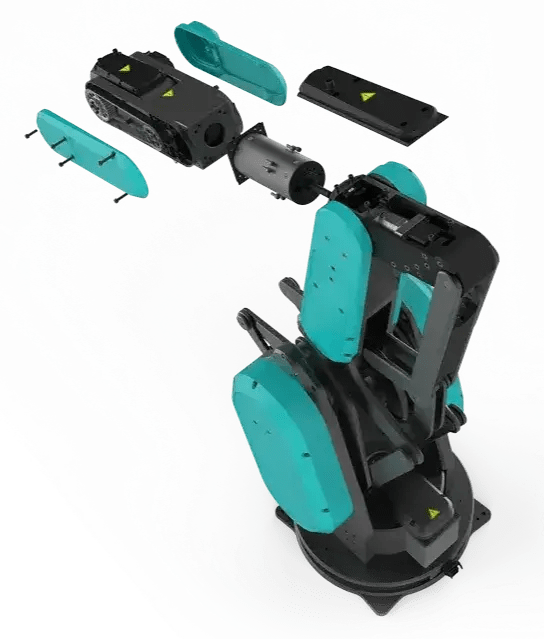
Intelligent software functions allow you to flexibly manage different machine manufacturing programs to suit different work orders. Seamless integration of machine functions such as automatic door opening and communication with clamping devices provides a particularly efficient solution for CNC machines. Additionally, improved axial acceleration increases efficiency when handling heavy parts or when using extended grippers.
CNC machines can be used immediately for metal processing.
Combined with automation modules for machine loading and unloading, the HORST1000 G2 provides a ready-to-use solution specifically designed for machine loading and unloading. “This allows rapid implementation on the production line, requiring only 15% of the typical project effort,” explains Jens Riegger. Existing interfaces to most CNC machine manufacturers enable seamless robot integration.
In metalworking medical technology, robots are used to produce surgical tools, where they efficiently load and unload CNC mills or lathes or prepare them for manufacturing processes. They are also used for loading and unloading machines in the metalworking automotive industry or to ensure consistently high quality in measuring and testing tasks.