How to reduce costs and take full advantage of traditional automated pick and place, test and dispense
Autor: Alexander Mühlens, Geschäftsbereichsleiter Low Cost Automation bei der igus GmbH
Robots have long been an integral part of the industry, including as machine assemblers, quality inspectors, and assembly assistants. However, many small and medium-sized enterprises (SMEs) are at risk of being left behind. Because often times we don’t even know where to start. What applications can you actually automate? And the investment costs are often too high and integration and operations seem too complex.
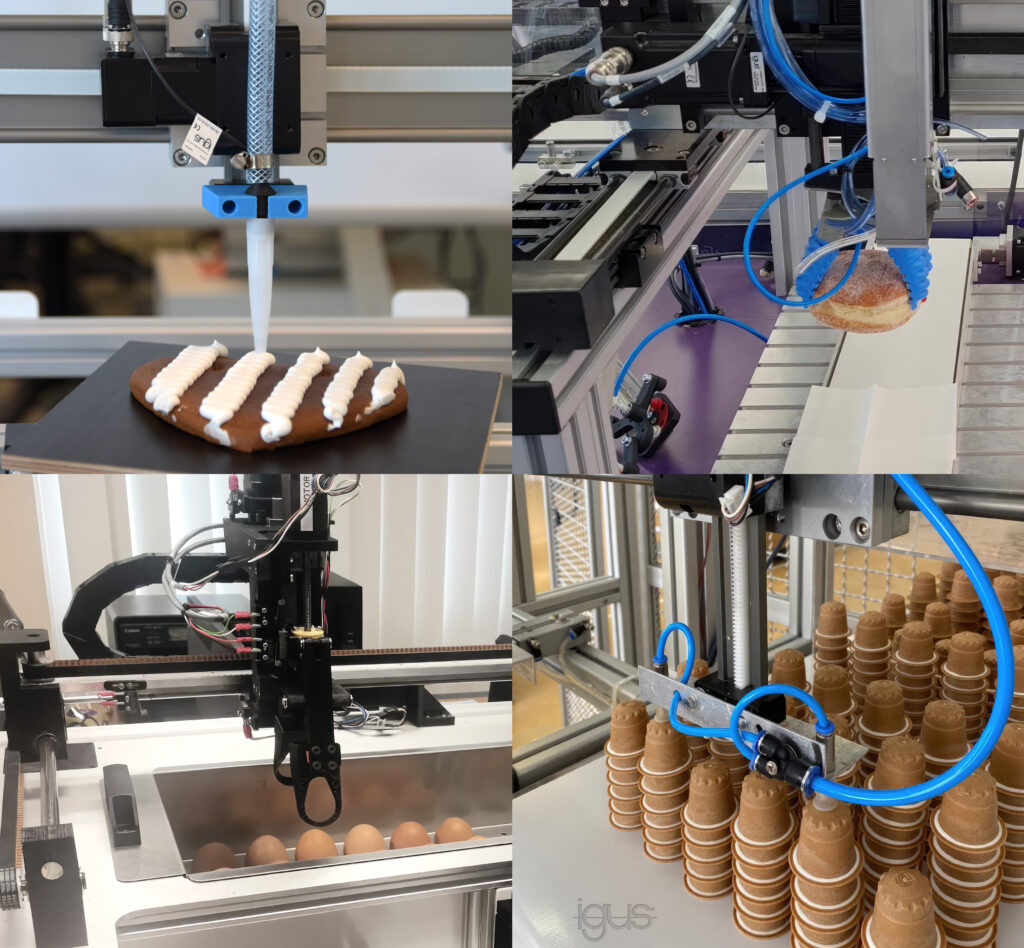
Picking, feeding, crushing or checking: there are a variety of monotonous, repetitive and laborious tasks that can be easily automated. Unfortunately, simply purchasing a robot doesn’t solve the problem. Ultimately, the entire system, consisting of components such as robots, vision systems, grippers, and sensors, must operate. But small and medium-sized businesses in particular often don’t know where to find solutions or what the right solutions actually look like. It’s also important not to start off too complicated. Manufacturer-neutral robotics market RBTX helps people interested in automation find the simplest and most cost-effective solutions to their tasks.
Complete solutions with over 400 real solutions
What’s special: Those interested can not only find robots and individual components on the market, but also gain insight into how others do them. As a source of inspiration for immediate imitation, you’ll find over 400 ready-to-apply automation projects through online exercises. From automated worm farms to Berliner pickers to agricultural robots that detect and remove weeds. Thousands of small and medium-sized businesses around the world have already implemented automation solutions from RBTX.com without any prior design knowledge. 95% of these complete solutions are available for less than 12,000 Euros. Low-cost solutions are proven to pay for themselves in just 3 to 12 months. Key applications include pick and place operations, quality inspection, adhesives and dispensing applications.
Efficient product handling with pick-and-place robots
Pick and place robots reliably transport objects from A to B. This is often a repetitive and time-consuming activity that offers many optimization possibilities within production. Whether machine assembly, palletizing, sorting or pre-assembly. The advantages of low-cost robotic solutions have sparked the automation trend in industries such as agriculture, food industry, medical technology, and trade. Pick & Place systems are increasingly being used in everyday end-customer applications such as vending machines.
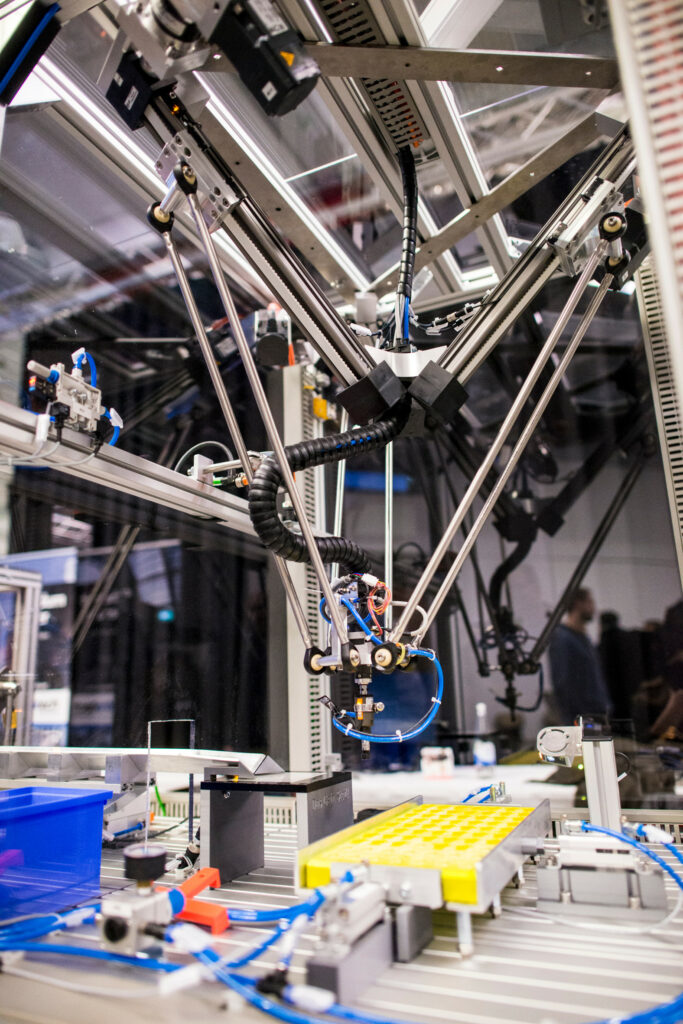
Different types of robots, such as articulated arm, delta or gantry robots, can implement different application scenarios. For example, gantry robots are used to grasp medications for transport to the dispensary, while SCARA robots act as “lab assistants” and are responsible for safely picking up and placing test tubes. It costs only 7,820 euros. Advantages of robotic systems: Parts are picked up accurately and with consistent quality and placed in the desired storage location. The process can be accurately repeated.
Automated quality inspection for greater precision and planning
Automated quality control ensures repeatable testing processes are performed efficiently and accurately. Application scenarios for robot testing are as diverse and individual as the work processes to be automated. Testing processes and characteristics are very diverse in practice, including surface testing, dimensional testing, and functional testing. For example, a robotic system was configured for automatic loading and unloading of a circuit board test station using RBTX.
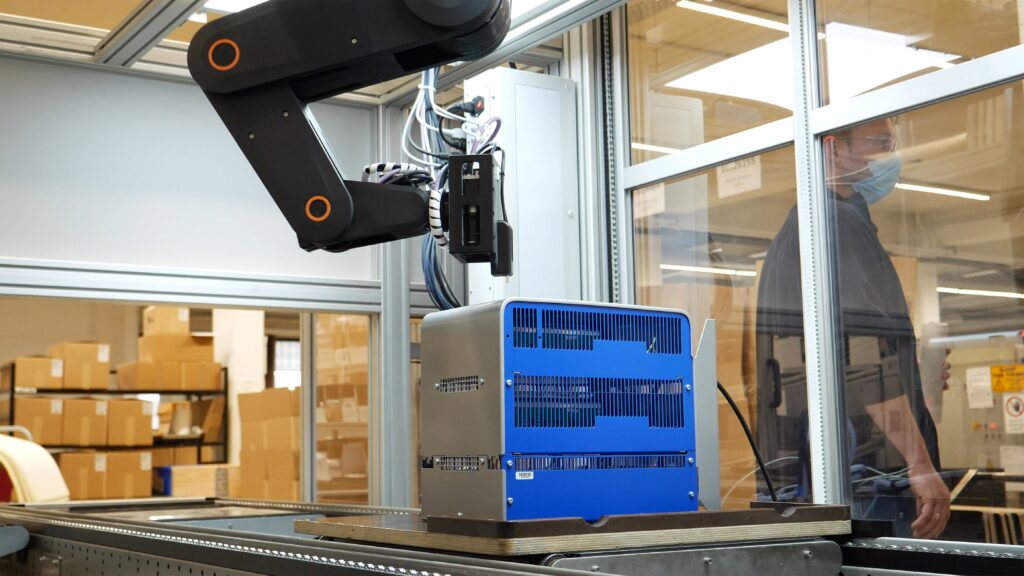
There is also a surface portal that controls individual clocks using cameras to visually confirm that the minute and second hands are moving. Robotic arms are also used in end-of-line testing, especially for chargers for electric vehicles. Using robots, you can efficiently streamline the testing process and plan it more effectively. Additionally, the robot operates around the clock without any loss of quality. Accurate and consistent measurement of the same process and test characteristics is guaranteed.
Attach and administer safely without wasting materials.
In addition to test and pick and place operations, the application of adhesives, sealants, paints and insulating foams can also be efficiently automated. In many cases, it is important to avoid wasting material and to ensure more precise gluing or dispensing. And you don’t need a robot with an investment cost in the six-figure range. Almost anything can be glued with a low-cost robot. Achieves a precision of approximately 0.5 mm. Another reason is job security. Robots can easily come into contact with chemicals and support non-ergonomic tasks. The bonding process, especially for small workpieces, requires a high level of concentration and precision. It is often important that the adhesive seals the part accurately. Automation through robots is clear. For example, using RBTX, a customer was able to quadruple the speed of applying sealant to metal parts, a critical step in production, by using an automated dispensing robot. The machine’s ease of handling allows even untrained employees to start using the robot right away.
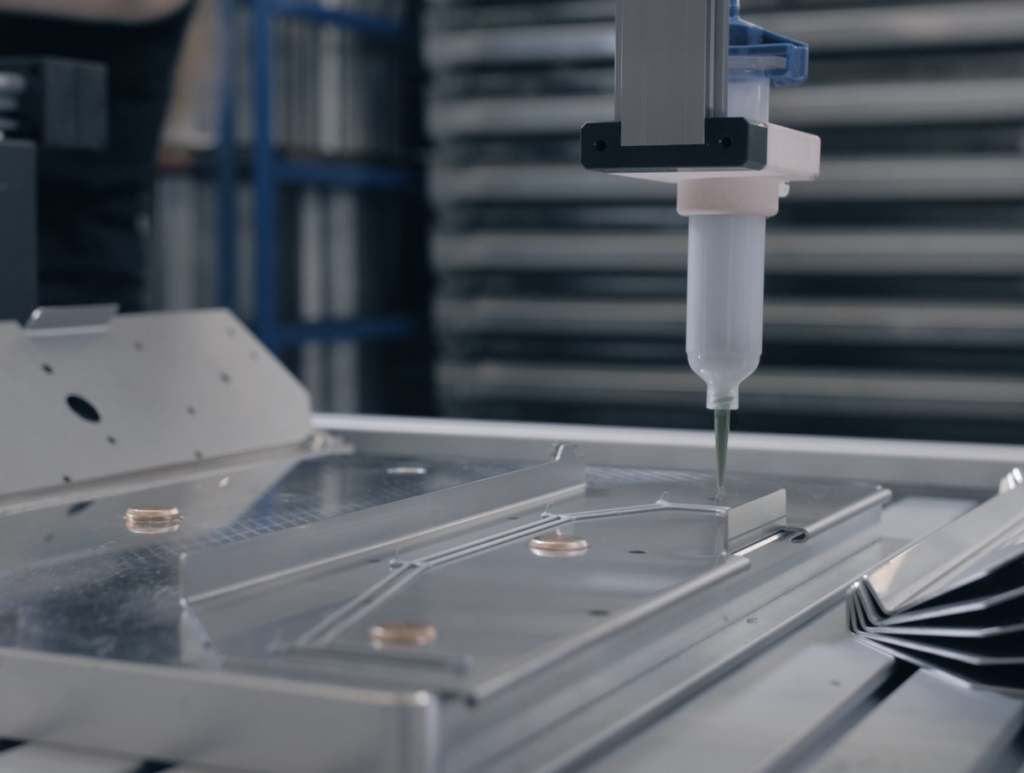
Depending on the application, a variety of robotic systems are available for gluing and dispensing. The self-dispensing robot configurator allows users to configure individual robotic solutions that automate precise gluing and dispensing processes in just a few clicks.
If you’re still looking for inspiration, you can find all the real-world application examples at RBTX.com (https://rbtx.com/de-DE/solutions).
RBTX is a registered trademark of igus GmbH.